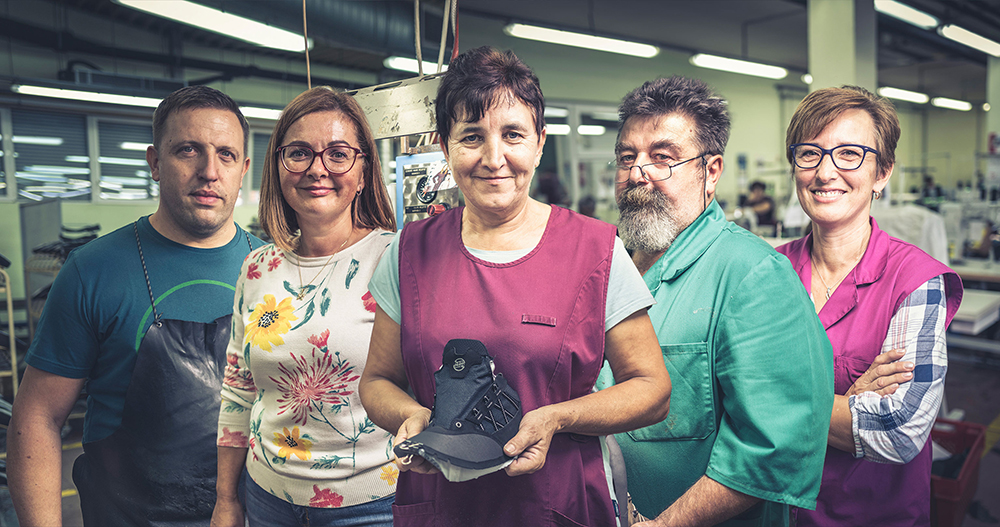
ハンワグ クロアチア工場
ハンワグのフットウェアはすべてヨーロッパで生産されています。しかし、なぜすべてヨーロッパで生産しているのか?
また、どのような職人のどのような技術が最高品質のフットウェアを生み出しているのかを探ります。
このシリーズでは、ヨーロッパ4か国にある5つのハンワグ工場を訪れ、どのように我々のフットウェアが作り出されているかを
探っていきます。そして、最高品質を作り出す4名のすご腕の職人も紹介します。エピソード1ではハンワグ最大の工場である
クロアチアの工場に潜入します。
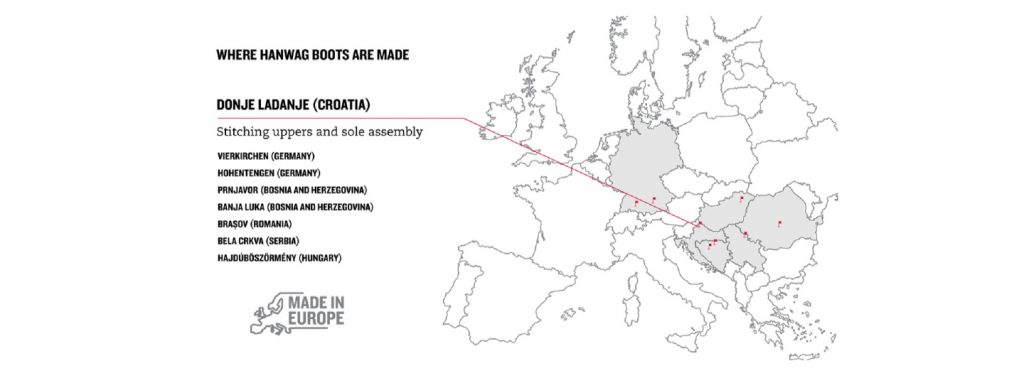
優れたフットウェアの中心地
ドイツのバーバリア地方にあるハンワグ本社から車で6時間ほど行くとクロアチアの北部に到着します。Varazdinの周辺はかつてフットウェア生産の
中心地だった場所です。今では数えるほどの工場しか残っていませんが、熟練の靴職人が多く残っています。Donje Ladanje地区のConsorsでは
約250名が働いています。Consorsでは1999年からハンワグのフットウェアを生産しており、最も重要な生産拠点の一つです。
Dudaと呼ばれているDubravka Pirovicは、ここでハンワグの生産が始まった最初の日から働いています。「ハンワグのほぼ全てのモデルの
アッパー部分の縫製は、ここの縫製部門で行っています」。Dudaが工場を案内しながら教えてくれました。30名あまりの女性が横並びに座って、
革の縫製をしたり、生地とライニングを縫い合わせたり、アッパーにクッション材を貼り付けたりしています。
「例えば、HANWAG Tatra Lightモデルは縫製だけで60の工程があります」とDudaが教えてくれました。
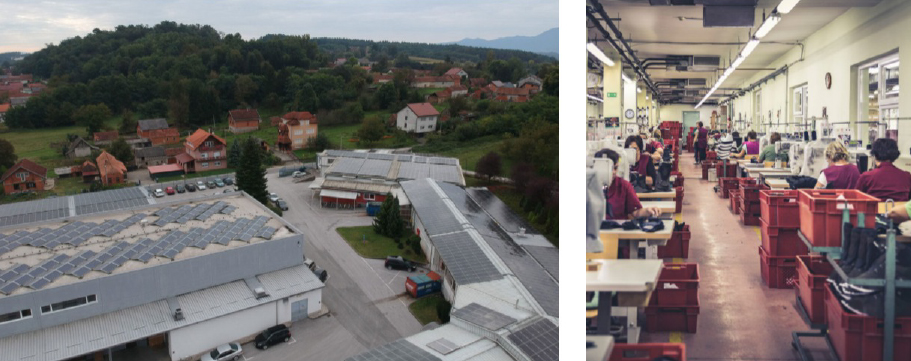
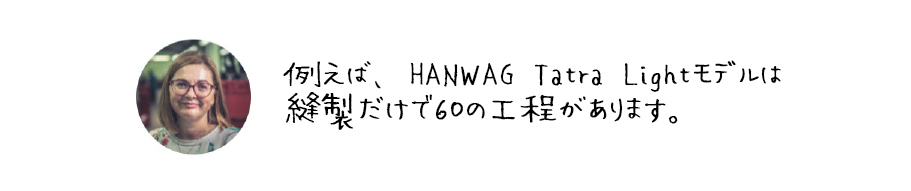
さらに次の40工程は「組み立て」です。ここではスタッフのほとんどが男性で大型の機械を操作しています。簡単に言うと、組み立てセクションで
アッパーがソールと組み合わされてシューズの形を成します。ほとんどすべてのハンワグモデルではセメント製法を用いています。
クロアチアで生産されたすべてのフットウェアは、中央倉庫であるドイツ北部のLudwigslustに送られます。
Donje Ladanjeは、最大のリペア工場でもあります。リペアが必要なハンワグシューズがヨーロッパ各地からこの工場に持ち込まれ、
ソールの張替えが終わったシューズは販売店を通してお客様へ戻っていきます。
ハンワグの品質を担う4名のスタッフを紹介します。
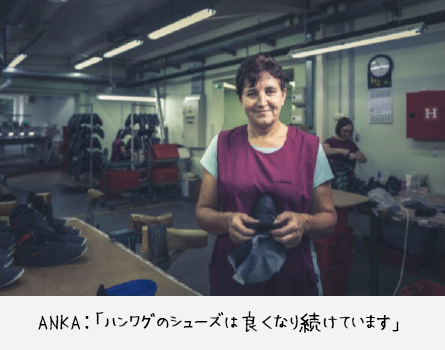
Ankaは木製のベンチの前に立ちアッパーに接着剤を施しながら話してくれました。「ミリ単位の正確さでクッション材を
取り付けます」。その後、いくつかの過程を終えるとまさにその通りに出来上がりました。Ankaは最大限の注意を払いながら
アッパーのレザー部分を検品し、接着剤がはみ出てないかを確認していました。
その後、ライニングがアッパーに取り付けられます。「しわにならないように、端がそろうように十分に気を付けなければなりません」。
そう説明してくれたAnkaのお気に入りはレザーライニングだそうです。「足のフィット感は他のものとは比べ物になりません!」
Ankaは2008年からConsorsで働いています。「昔に比べて働く環境も良くなっています。特に接着剤のにおいは前ほど強烈ではなくなっています。
もちろん、シューズも年々よくなっていて、特にライニングのフィット感は最高です」。
Ankaは靴づくりをしていて「このシューズはどこに行くんだろう??」と考えることがよくあります。彼女自身も家族と
ハイキングすることが大好きで、工場からほど近いところには、山道がブドウ畑に覆われたIvnscica山(1,059m)もあります。
「ここでは、多くの人が高級なハイキングブーツを買えるわけではありませんが、誰かがハンワグを履いているのを見ると
とても誇らしく思います。私がそのシューズを作ったのよ、と」。
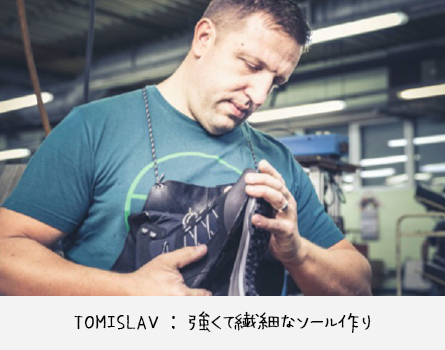
それほど重くは見えませんが、Tomislavが組み立てるシューズの中には2キロのラストが入っています。37才のTomislavは、
棚から1足を取り出しインソールに接着剤でアウトソールを注意して貼り付けます。そこから圧力をかけて接着剤を完全に
固定すると、シューズを圧着機から取り出し、完全に接着されているかを確認します。毎日350足以上のシューズがTomislavの
手によって組み立てられます。とてもハードな仕事です。
「でもこの仕事を楽しんでいますよ」。彼はきっぱりと言い切りました。Tomislavの父Josipはプロダクションマネージャーとして
この工場で働いていました。「17才の時に父に会いにこの工場に来たのですが、すぐにこの仕事が気に入りました」。
そして学校を卒業した後すぐにHanwagの組み立て部門で働き始めました。縫製部門は女性がメインで働いていましたが、
組み立ては男の仕事です。
彼のもっとも重要な相棒はマシーンたちです。大量の一般的なプレスから、空気の入ったソールのプレスまでを行います。これは主にローカットの
シューズで、その構成部品をプレスで圧着します。「どのモデルにプレスをかけるにしても、圧は正しくある必要があります。機械は調子が良くない日も
あって、その時は易しく扱う必要があります。特に休み明けはやる気がない時があります。そういう時は何日かかけてウォームアップしてあげます」。
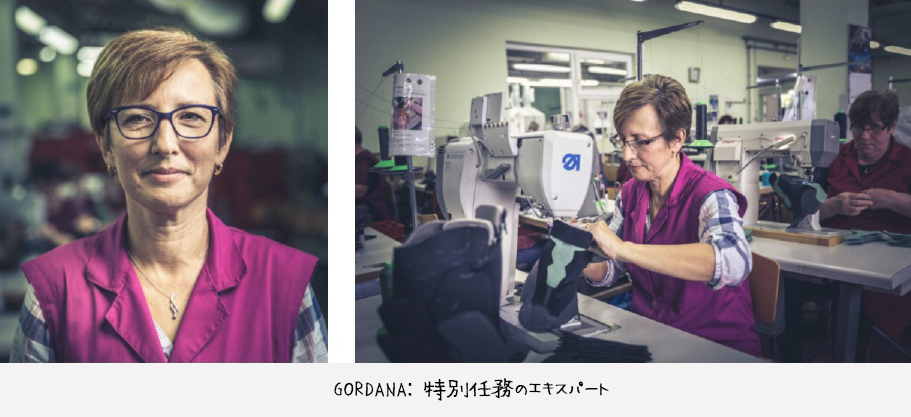
Gordanaは1996年からConsorsで働いています。彼女は人生の半分をフットウェアのアッパーの縫製に費やしています。今ではスペシャリストとして
Alverstoneなどの難しいモデルを任されています。「アッパーは多くの異なる部材を縫い合わせて出来ています。そして、Banks Lowなどの
ローカットモデルはステッチが比較的少なく出来ています」。とGordanaが教えてくれました。
Gordanaは、フットウェアが以前よりも面白いものになっていると感じています。「カラーは増え、シューズのタイプも変化しています」。
2016年からGordanaは新しいソーイングマシーンを使い始め、いくつかの縫製が自動になりとても楽になりました。
「働く環境もどんどん良くなっています。ほとんどのメンバーは顔見知りで長く一緒に働いていますからね」。
Gordanaの2人の子供は彼女と同じ道を歩むことはないと言います。「二人とも今は大学で学びながら全く違う道に進む予定です」。
Gordanaはいつまでハンワグで働くつもりなのでしょうか?「定年まで働くよ」彼女は笑顔で言いました。クロアチアでは女性は働き始めてから
41年で定年になる制度があります。なので、まだしばらくはGordanaの手によって出来上がるシューズを見れそうです。
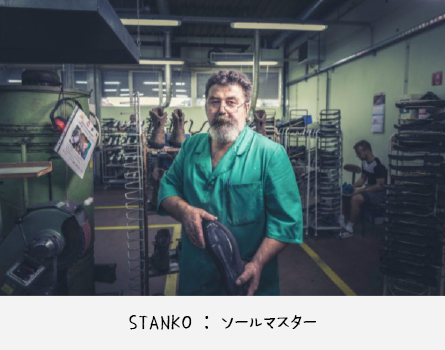
Stankoの任務もTomislavと同じく組み立てです。資格を取得しているシューメーカーは靴作りの工程を完全にこなすマスターであり、
それこそが彼がソールマスターとして知られている由縁です。Stankoに会った時、彼はラバーソールを貼り付けるために
様々なモデルのインソールを準備していました。
「必要な時はいつも私がヘルプに入ります。私に与えられる任務は様々ですが大きなやりがいを感じています」。と
Stankoは教えてくれました。彼は4年間他のシューズ工場で見習いを行った後、1999年からConsorsで働いているので、
ハンワグの立ち上げから参加していることになります。「見習いの頃は、約10,000人が工場で働いていました。
本当に多くのフットウェアブランドがありましたが、ほとんどが廃業していきました。そんな中で今の仕事につけて
本当に幸せです」。Stankoは笑顔で打ち明けてくれました。
見習い期間中、Stankoは普段使いのフットウェアを作っていました。そして今はテクニカルなアウトドアシューズを作っています。
「ハンワグの生産は本当に興味深いです」Stankoは流ちょうなドイツ語で話してくれました(以前彼はオーストリアに住んでいたそうです)
「マスターしなければならない行程は数多くありますが、その分、シューズの造りは素晴らしいものです」。
22年働いて56歳になった今でも向上心に溢れています。「毎日が学びです。常に学び続けています」。
あなたから学びたい人はどうしたらいい?「そうだね、ここに来てソールマスターの仕事ぶりを実際に見てください!」。
「MADE IN EUROPE」の次の目的地はハンガリーのハンワグ工場です。